1.Raw Material Preparation: Materials for making PVC granules are PVC resin, plasticizers, stabilizers, lubricants, and other additives. These materials are carefully measured and prepared according to the desired formulation according to customers’ requirement.
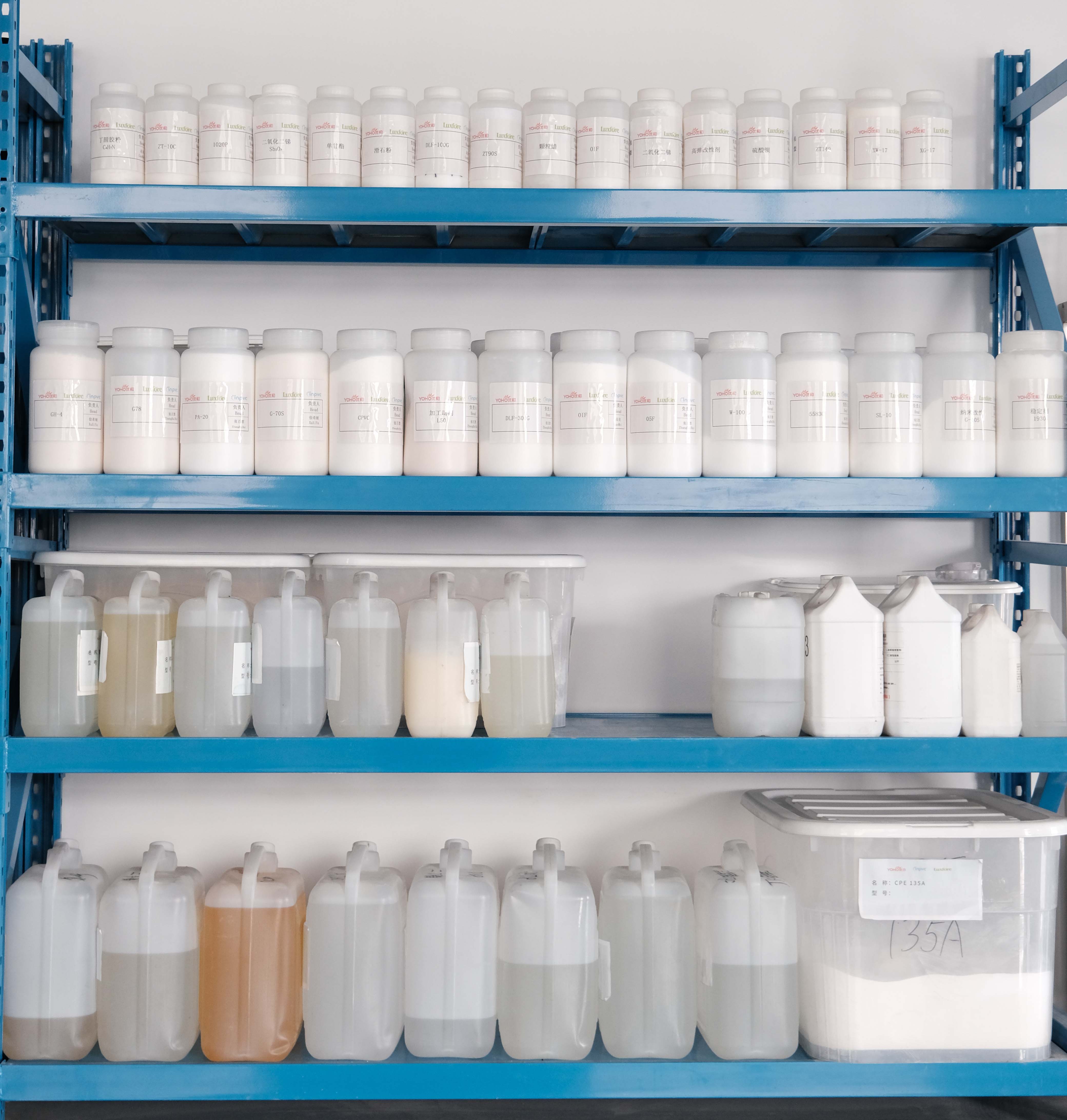
2.Mixing: Raw materials are mixed in high-speed mixers to ensure a uniform blend. The mixing process typically involves both dry blending and heating to achieve a homogeneous mixture.
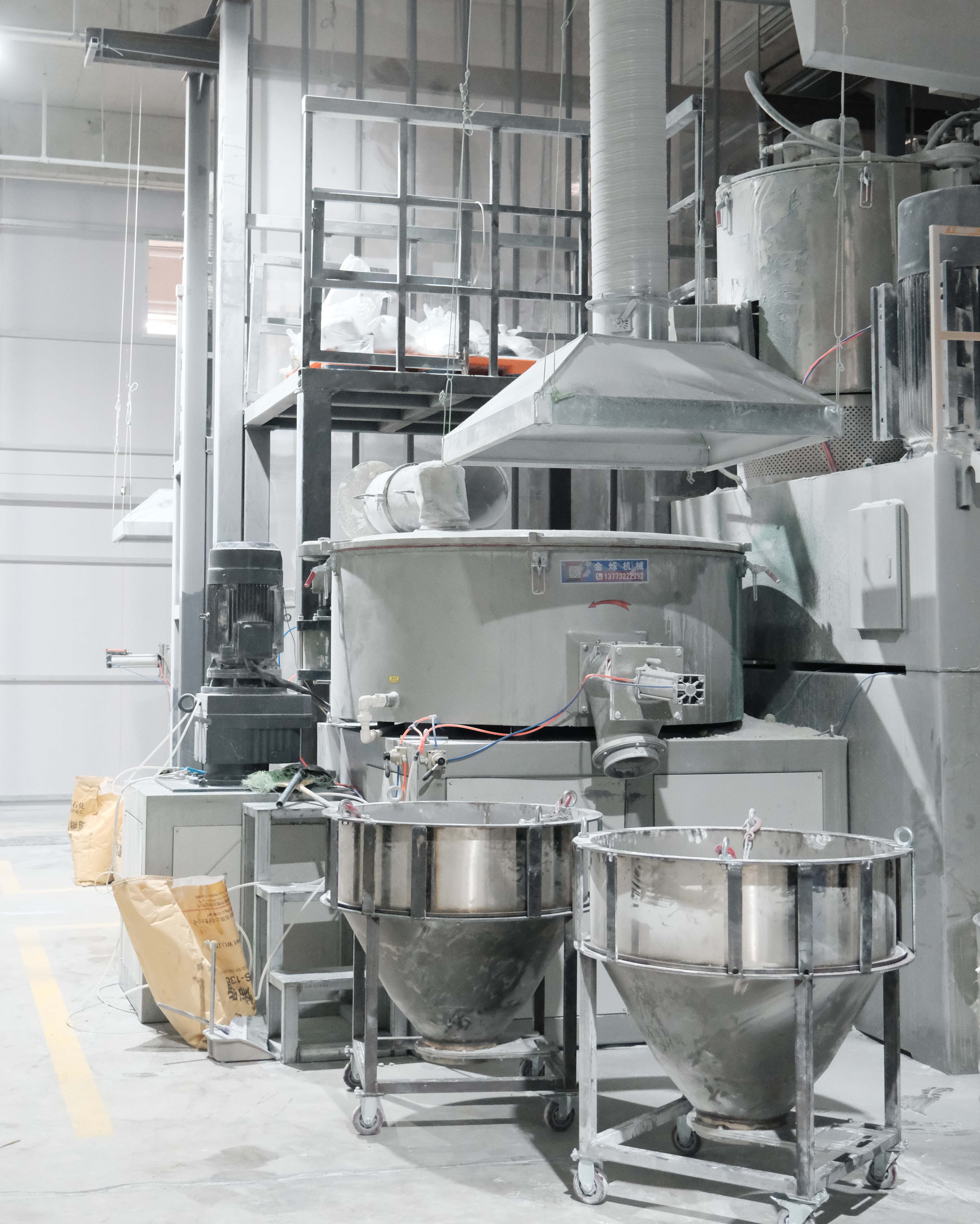

3.Compounding: The mixed raw materials are then fed into extruder, where they are melted and compounded. The extruder heats the mixture to a specific temperature, causing the PVC resin to melt and the additives to blend thoroughly. This step is crucial for achieving the desired properties of the final product.
4.Extrusion: The molten PVC mixture is forced through a die to form continuous strands or sheets. The shape of the die determines the shape of the extruded product.
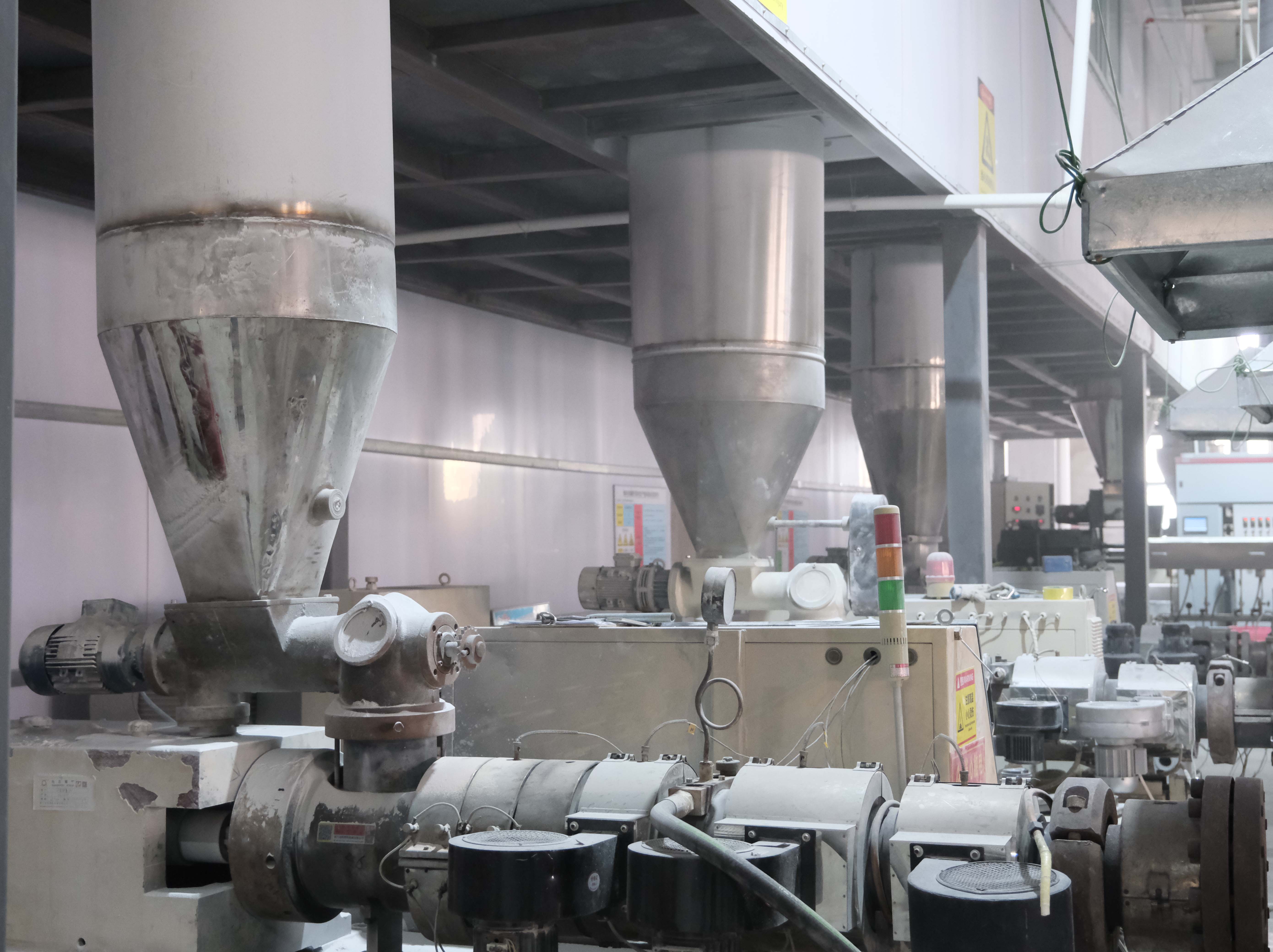
5.Cooling: The extruded PVC strands or sheets are cooled rapidly, usually in a water bath, to solidify them. This cooling step helps in maintaining the shape and integrity of the material.
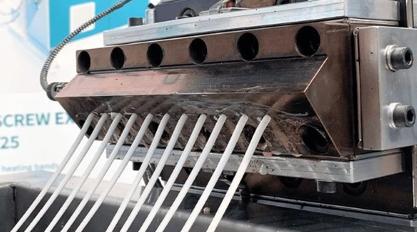
6.Pelletizing: The cooled PVC material is then cut into small granules or pellets. This can be done using various types of pelletizing equipment, such as strand pelletizers or die-face pelletizers.
7.Screening and Classification: The PVC granules are screened to remove any oversized or undersized particles. This step ensures that the granules are uniform in size and shape.
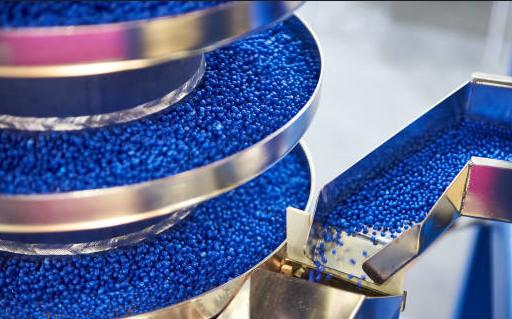
8.Packaging: The final PVC granules are dried and then packed into bags, containers, or bulk storage systems for distribution and sale.
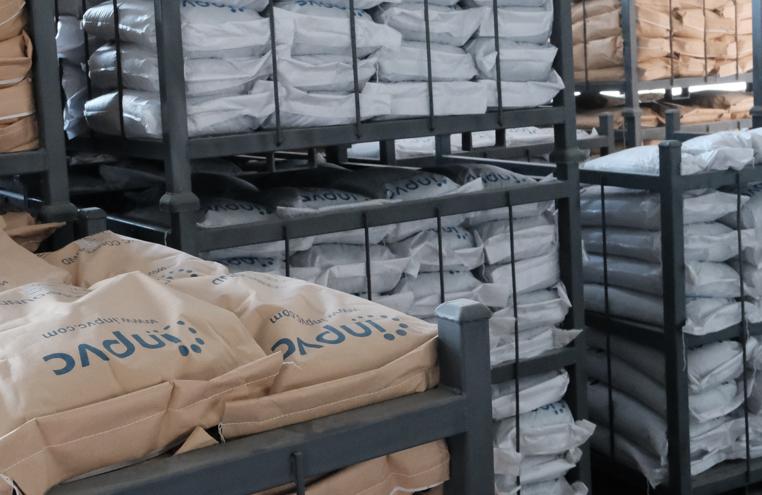
9.Quality Control: Throughout the manufacturing process, quality control measures are implemented to ensure that the PVC granules meet the required specifications. This includes testing for physical properties, chemical composition, and other relevant parameters.
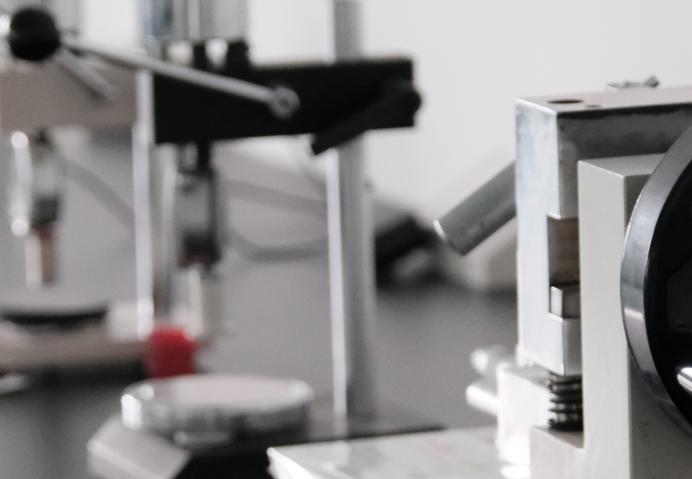
Post time: Jul-11-2024